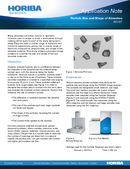
If it can’t be grown, it must be mined...If it was mined, particle size matters.
The USGS (United States Geological Survey) Mineral Commodity Survey for 2015 lists more than 90 different minerals from abrasives to zirconium. Of these, 14 have a U.S. mine production of more than $1 billion in 2014.
Extracting useful minerals is an arduous and technically demanding process. First, any material on top of the deposit, known as overburden, must be removed or tunneled through. In the next step, the ore is blasted or cut and loaded and hauled to the mill for the secondary crushing and grinding which prepares the material for its intended use.
In many cases, the valuable minerals are mixed with gangue, commercially useless material, and the ore must be separated. The first step of many separation processes is comminution (size reduction) followed by classification (separation by particle size) either for further grinding or the next step, concentration of the ore. During comminution, ore must be ground such that the particles are small enough that each particle consists of primarily one mineral. These particles are then separated to concentrate the mineral product.
Gravity separation relies on differences in material mass to separate minerals. Methods include jigs, sluices, spirals, shaking tables, fine particle separators, and hydrosizers and cyclones. Gravity separation is separation based on weight only and is directly affected by particle size since volume is proportional to weight.
Jigging uses pulsed water flow or a similar process to push up ground material. Heavier and larger particles will sink more quickly between pulses and thus tend to the bottom of the jig. Thus, uniform particle size is important to ensure separation by density and not size. In addition, jig operation (length of water pulses) and design will depend on the size of particles being separated. Sluices and spirals rely on the difference between viscous drag and buoyancy for particle separation. This difference is directly related to particle size. Gravity tables use a vibrating platform to separate by particle size and specific gravity. Thus, narrow size distribution feeds result in better separation.
Here the material is separated by surface chemistry. Bubbles flowing through a slurry or suspension will tend to stick to particles with a hydrophobic surface and cause the particles to float to the top of a froth for recovery. Often, particle surfaces are selectively modified so that mineral surfaces are hydrophobic while gangue surfaces are hydrophilic. Particle size is important to the process efficiency. Overly fine particles may be entrained in the bubble flow regardless of surface chemistry, reducing the effectiveness of separation efficiency. Overly large particles will tend to sink regardless of bubble attachment.
Froth at top of flotation tank.
The behavior of a particle under electrostatic or magnetic fields can be exploited to separate particles by type. These fields will induce charges (or magnetism). The resulting forces will cause particles to move depending on particle mass. Thus small particles are moved further than large particles. Furthermore, particle charge is a surface phenomena and the larger surface area of fine particles will tend to have a higher charge. These size effects can lead to separation by size rather than composition. As such, a narrow size distribution often, but not always leads to better separation.
The final product is often graded and sold as-is or for further processing. Typical customers will want a particle size in order to ensure that their process is optimized. Thus, in the all important step of selling products, many mines will control particle size. In some cases, particle shape is important as well.
This sign outside of the closed Lackawanna Coal mine indicates that particle size has been important in the final shipment of mine products for hundreds of years.
Choice of particle size analysis technique is a function of the goals of the analysis. Many of the particles encountered in mining are characterized by sieves (classifiers). These are screens with a known opening (mesh) size. Particles smaller than that mesh size will pass through the screen and larger particles are retained. Analysis is performed by building a stack of sieves and shaking the stack, either manually or with a sieve shaker. Material caught on each screen is then weighed and the data combined to extract size distribution. The sieves are then cleaned for reuse.
Sieves have a long history and low initial cost. Sieve results are often strongly affected by operator technique. This effect is somewhat mitigated by sieve shakers (albeit at an increase in cost). In addition, sieves are delicate and mechanical shock can change the size of the screen openings. Furthermore, since the particles directly contact the screen surface, sieves will wear during correct use (or cleaning). As the sieve openings expand, the obtained results will drift over time with little or no indication to the operator that they are no longer accurate. Sieve analysis is widespread due to its longevity and intuitive use. Newer technologies have considerably improved the accuracy, reliability, and time of analysis - all providing improved margins for producers - leading to sieves being replaced in many companies and industries.
Damaged sieve mesh that will give misleading size results
As particle size decreases, sieving and/or dynamic image analysis becomes more arduous or impossible and laser diffraction becomes the technique of choice. Once the particles are too fine for image analysis - roughly several microns - they are best analyzed by laser diffraction instruments such as the LA-960V2 and LA-350.
Idealized scattering from a round particle.
Dynamic Image Analysis
Direct Imaging Particle Analyzer
Nanoparticle Analyzer
Centrifugal Nanoparticle Analyzer
Laser Scattering Particle Size Distribution Analyzer
Laser Scattering Particle Size Distribution Analyzer
BET Flowing Gas Surface Area Analyzers
BET Surface Area Analyzers
Simultaneous Multi-Laser Nanoparticle Tracking Analysis (NTA)
Do you have any questions or requests? Use this form to contact our specialists.